2024/04/26(金) - 17:30
台湾・台中のジャイアント本社工場を訪問
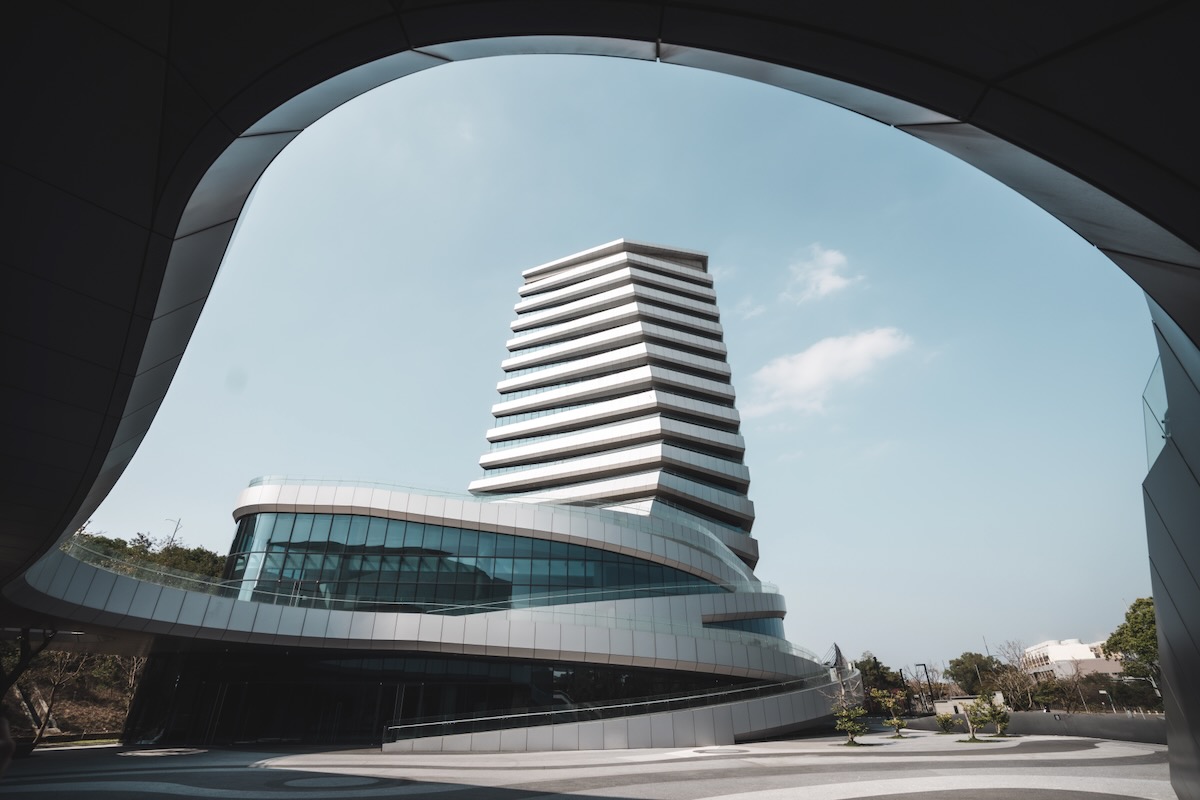
日本を出国して空路で3時間、台北の松山空港からはクルマで2時間。ジャイアントをはじめとする各ブランドが本社工場を置き、台湾の、いや世界の自転車産業の中心地と呼べる台中(現地発音はタイチュン)は、日本から半日もあれば着く場所にあるのだ。
ジャイアント本社で開催されたグローバルローンチに馳せ参じたのは、シクロワイアード編集スタッフの磯部。5年前に落成したばかりだという美しいビルは、台湾の先進ブランドが集まる真新しい工業団地の中でもひときわ目立っていて、併設されたサイクリング・カルチャー・ミュージアムなども含めて世界ナンバーワンブランドであることを象徴するものだった。
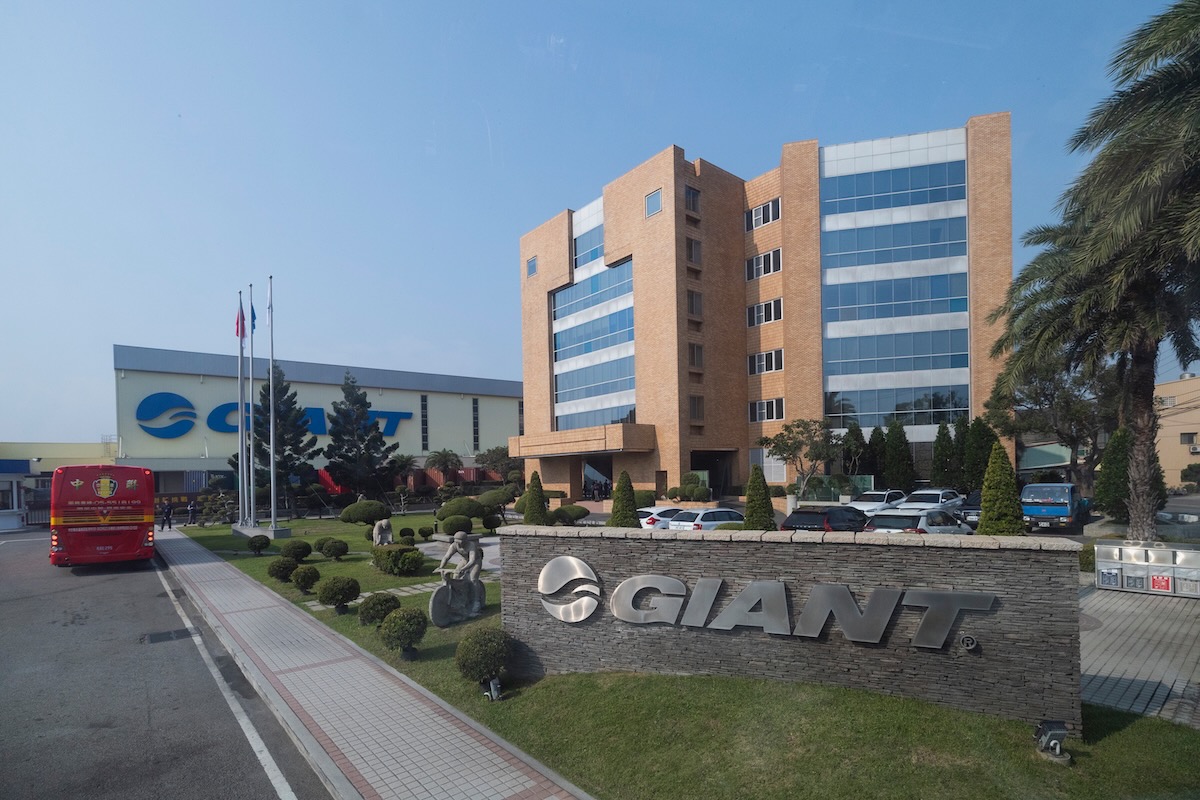
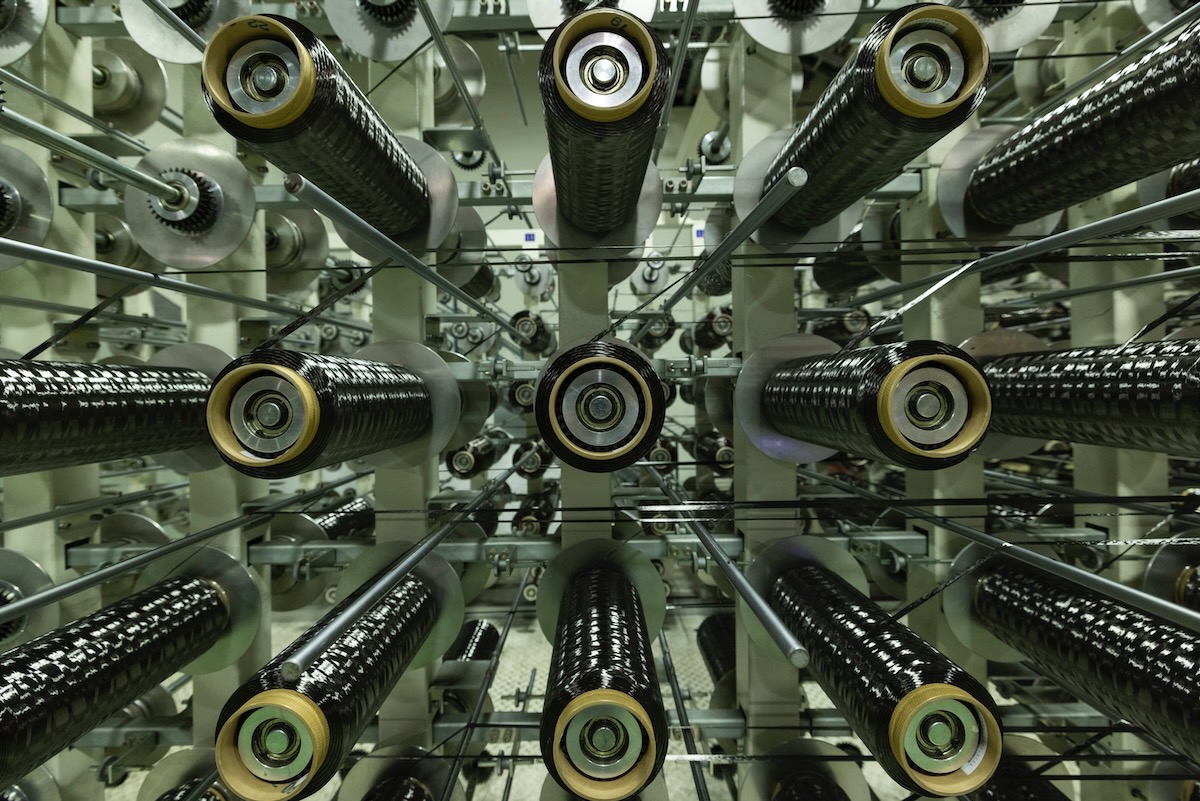
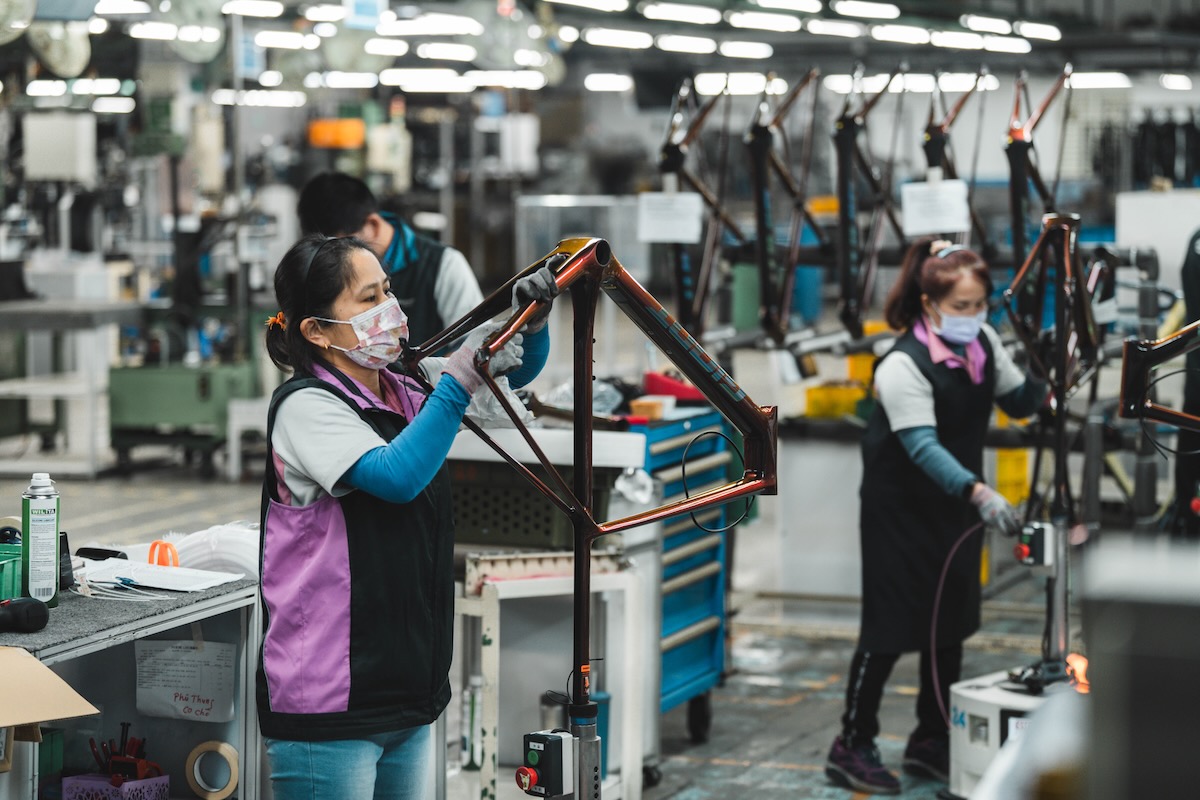
前章でも記した通り、これまでジャイアントはフランスやイタリアでグローバル発表会を開催してきたが、台湾本社に世界中のジャーナリストを招くのは初めてのこと。世界のロードバイク設計を変えたフラッグシップモデルの第10世代という節目において、TCRが生み出されたその地で、開発に携わった人々と話し、どう生産されているのかを見ることに大きな意味があった。
カーボンシート(プリプレグ)から生産する自社ファクトリー
新型TCR生産の全てを見学
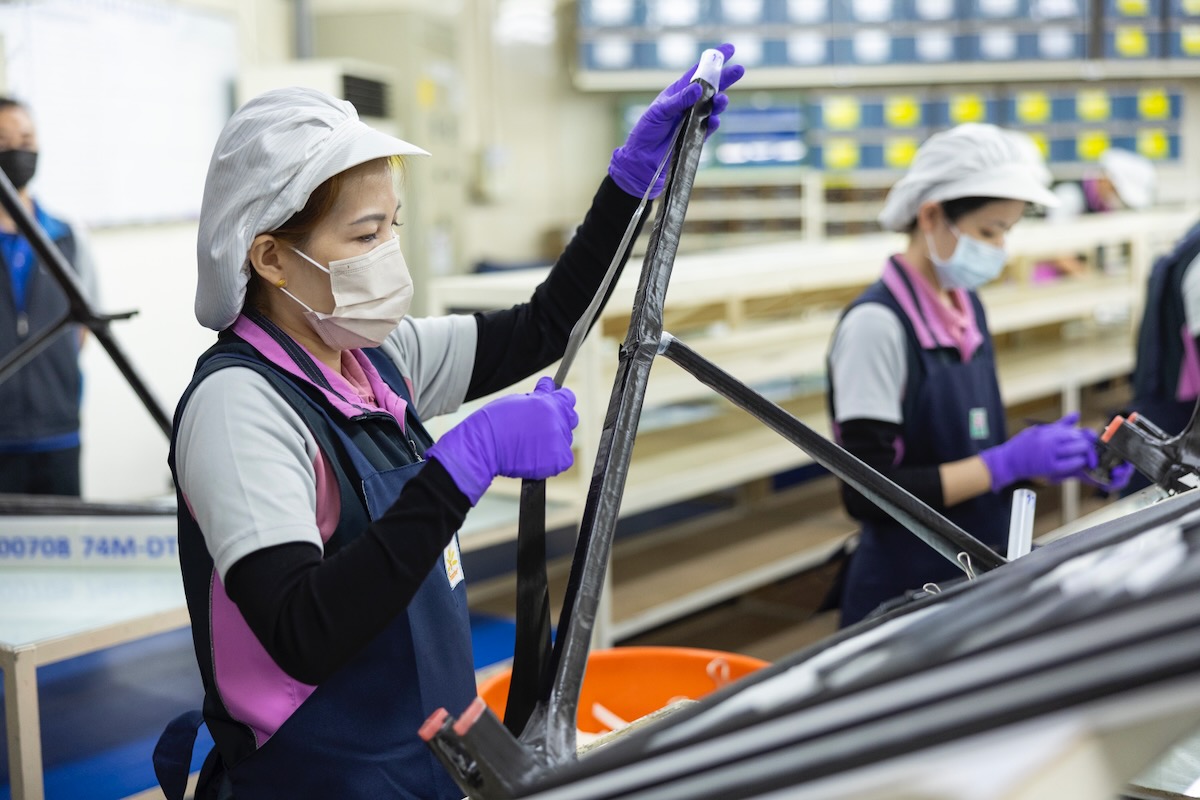
我々メディアチームが訪問したのはジャイアントの旧本社に併設されている巨大工場だ。ジャイアント・台湾・マニュファクチャリング(GTM)と呼ばれ、世界に9つあるジャイアント工場の中でもハイエンドアルミとカーボン製バイク製造に特化した中心的存在だ。9つの工場を合わせれば年間500万台以上もの自転車が日夜送り出され、そのうちの70%がジャイアントグループ、30%が他社へのOEM生産なのだという。
今回見学が許されたのは新型TCR ADVANCED SLの製造工程だ。ジャイアントが誇るカーボンシート製造に始まり、シートのカット、カーボンレイアップ、品質テスト、ペインティング、そして組み付けまで。今回新採用されたカーボンシートの製造工程「コールドブレードカッティング」など写真撮影禁止の部分も多かったものの、まさに製造工程の最初から最後までを目に焼き付けることができた。
以下はスライドショーで新型TCRが形となっていく様子を紹介します。各写真の説明とともにお楽しみを。
開発のキーマン、ニクソン・ファン氏が語る新型TCR
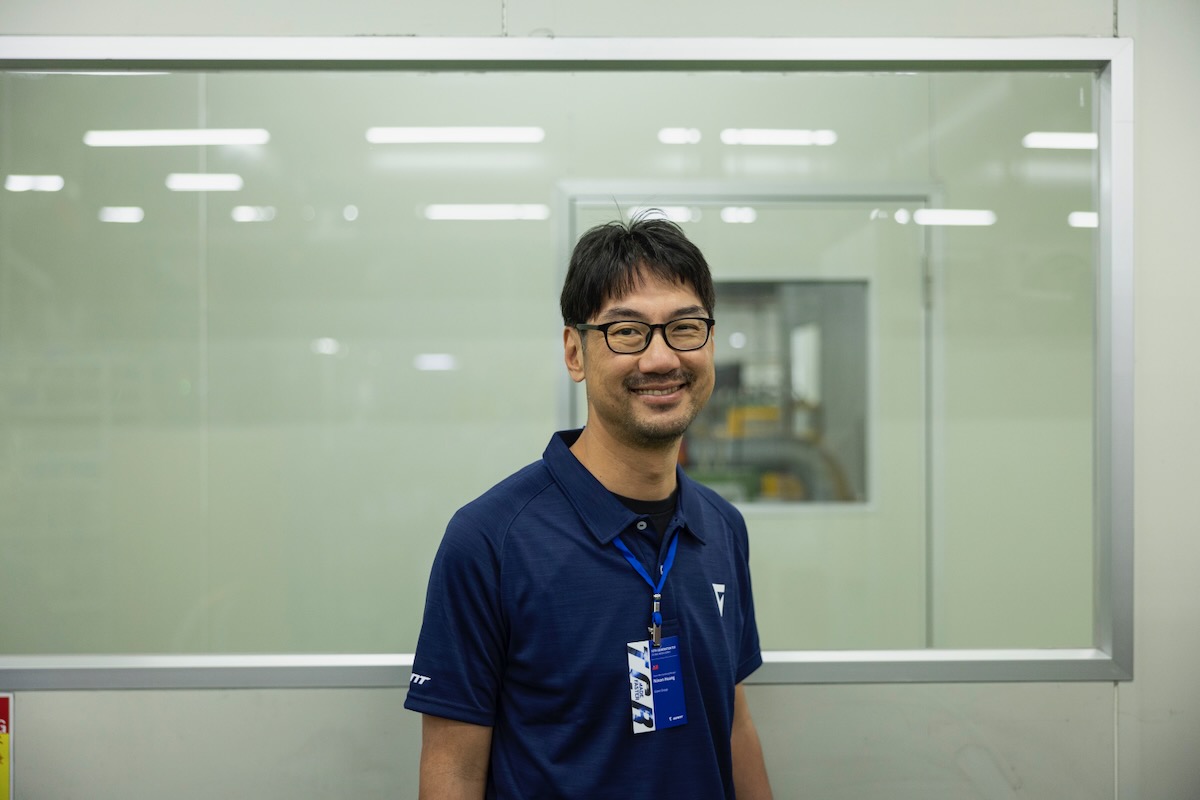
TCRの、そしてジャイアントのロードバイク開発を主導するのがニクソン・ファン氏だ。ニクソン氏は5世代前からTCRの開発に携わり、今は開発マネージャーとしてDEFYやPROPELにも深く関わるキーマン。筆者は発表会に帯同した彼と話し、新型TCRのより詳しい話を聞くことができた。新しい製造技術は何がすごいのか?第10世代TCRに込められたメッセージとは。
CW:カーボンシートの切り出し工法を、従来のレーザーカッティングから「コールドブレードカッティング」製法に切り替えた(ADVANCED SLグレード)ことが性能進化の大きな理由の一つと語られました。具体的にはどのようなメリットがあるものなのか説明してもらえますか?
ニクソン:「コールドブレードカッティング」自体は2世代前のTCRを開発する際、プロトタイプ製造の際に初めて試験投入したものです。ただしその時点ではあまりにもコストが掛かりすぎるため本採用を見送っていましたが、今回遂に導入することができました。
コールドブレードカットのメリットは、シートを焼き切るレーザーカットとは違い、過剰な熱による変形の恐れがなくなり(変形公差を意図する必要がなく、結果的にシートの重なりを減らすことができる)、カーボンシートの数を減少できることにあります。

カーボンシートを減らすことはつまり、シート同士の重なりを減らすことで重量削減と剛性強化に繋がります。成型時に空気が入り込むことも防げますし、メリットが大きいのです。フロント三角が従来の3ピースから完全な1ピースになったことも剛性強化に貢献しました。
2世代前のTCRまでは型抜き方式、先代ではレーザーカット式、そして今回はコールドカット式と、我々は常に製造方法自体も見直しを図っていますが、これは明らかに自社工場を持つメリットです。見た目自体は先代モデルとの差は大きくありませんが、カーボンシートの製造から積層プロセス、レイアップスケジュールまで、中身は完全に進化しているんです。
ちなみに、最初に説明した先々代TCRのコールドブレードカッティング試作モデルは私が現在所有して乗っています(笑)。
CW:フレームセットのルックス自体は歴代あまり変わっていませんよね。各社共にフレームデザインが似通ってきている中、TCRは独自性を強く保っているように思うのですが、この意図は?
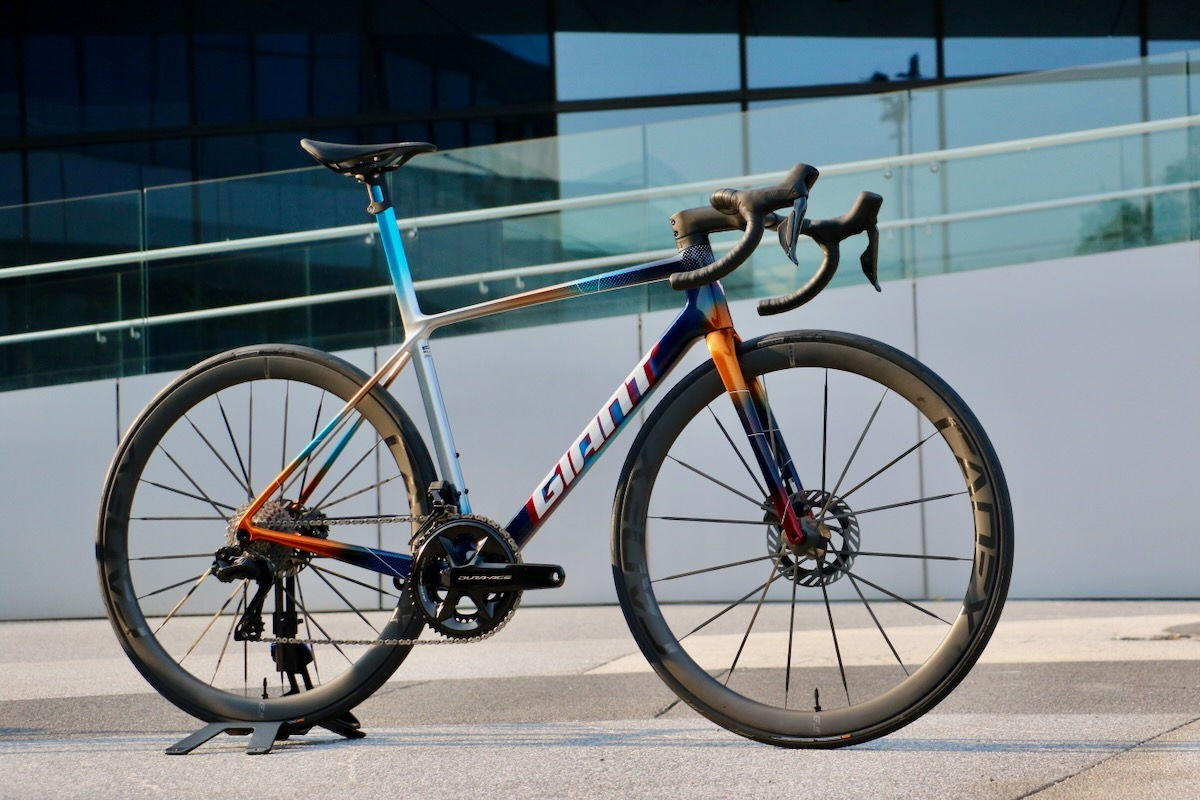
ニクソン:これは見た目ではなく、軽さを第一に、重量剛性比とエアロダイナミクスの性能バランスを突き詰めた結果なのです。いま現在、各社でシートステーとシートチューブの交点を下げたコンパクトなリアバックが採用されていますが、あのデザインは前方投影面積が小さくなることでエアロダイナミクスに優れる一方、構造体として弱くなるため補強材が必要となり重量がかさみます。
やや重量を犠牲にしてでもエアロを優先したPROPELにはコンパクトなリアバックを採用したように、デザインも適材適所。重量剛性比を最重視するTCRに対してはこのデザインこそ最良であるのです。
CW:プレゼンテーションでは快適性についてのアナウンスがありませんでしたが、その部分は加味されているのでしょうか?
ニクソン:もちろん軽さと重量剛性比がメインターゲットですが、快適性についても忘れてはいません。ADVANCED SLでインテグラルシートポストを残しているのも軽さと快適性を両立するためですし、タイヤのワイド化とチューブレス化による乗り心地向上も大きな要素です。最大タイヤクリアランスは先代の32mmから33mmと微増し、余裕をもってワイドタイヤを装着できるようになりました。ADVANCEDフレームはそもそもカーボン素材自体がややしなるので、ISPでなくとも快適性は担保されています。
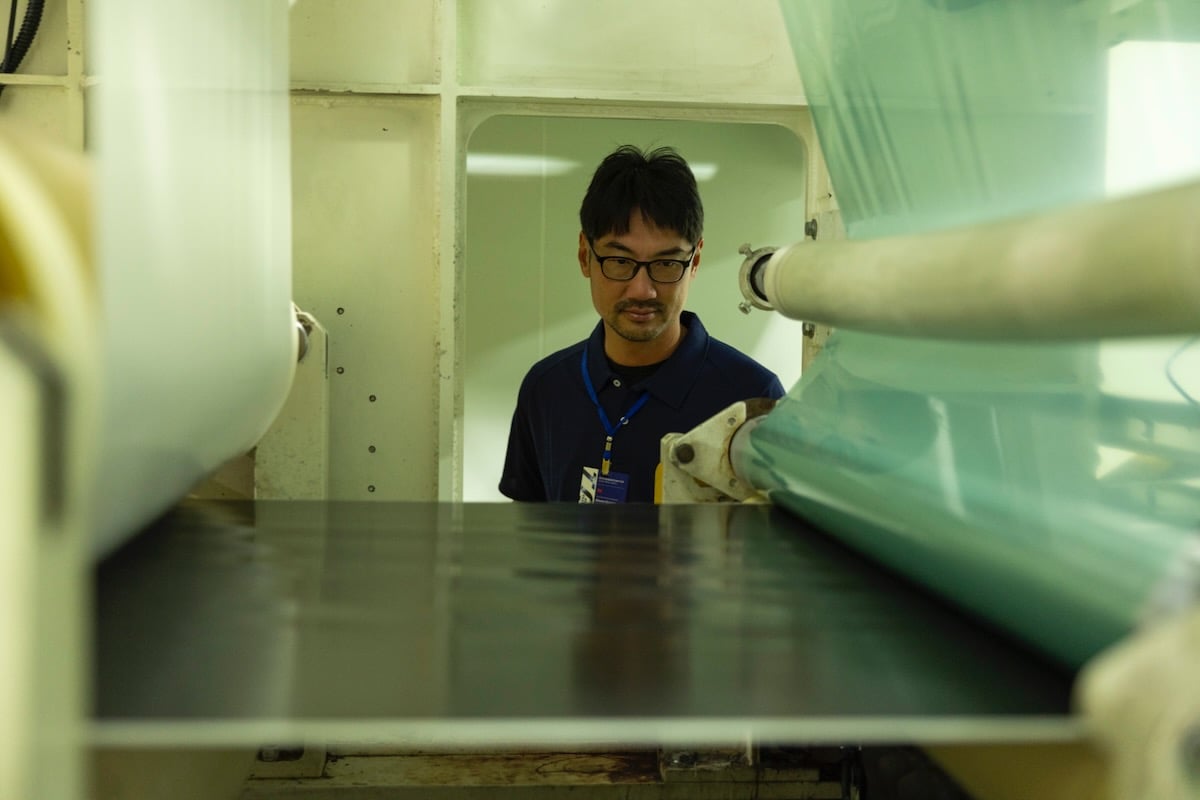
CW:これでPROPEL、DEFY、そしてTCRとジャイアントのロードバイク3モデルが全てモデルチェンジを果たしましたね。特にTCRは第10世代ということで、意味も大きかったのでは?
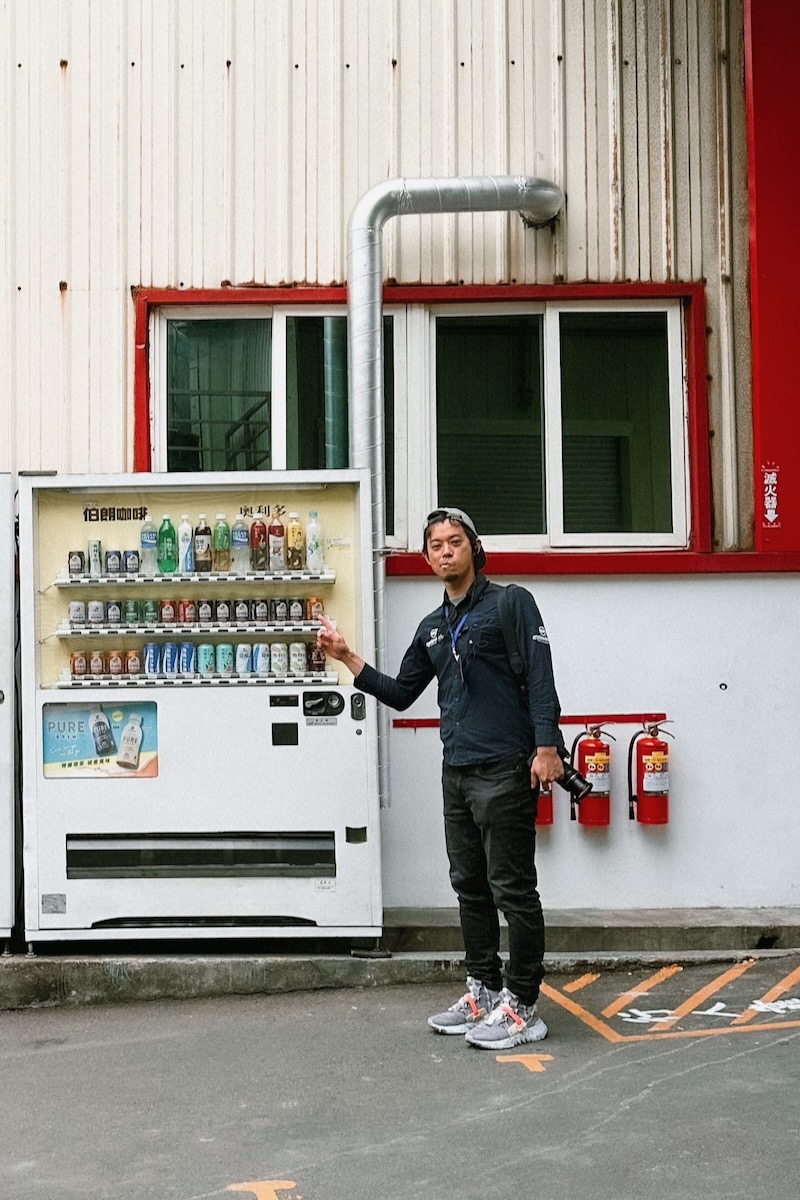
これまで(ジャイアントがサポートする)ジェイコ・アルウラーはほぼ100%PROPELを使っていましたが、早速クライマーたちがTCRを駆り勝利を挙げています。ジェイコよりもクライマー率の高いエキポ・ケルンファルマではメインバイクになる予定ですし、日本のシマノレーシングにも供給されると聞いています。嬉しいことですね。
PROPELは純粋にエアロダイナミクスを高め、登りもこなせる軽さとプロのパワーに負けない剛性を備えたレースマシン、DEFYは一般ユーザーに最適な快適性と剛性バランスを重視したエンデュランスモデルで、TCRは最軽量かつ最高の重量剛性比を備えたトータルレースバイクです。
台湾も同じですが、日本ではヒルクライムが非常に盛んですよね。そういったイベントやレースには最適なバイクですし、アップダウンが連続するコースでもTCRの走りの軽さは光ります。かつてないほど高速域で、フルガスで走る場面に最適なTCRですから、ぜひ日本のサイクリストの皆さんにも乗ってもらいたいと思います。
提供:ジャイアント・ジャパン / text:So Isobe